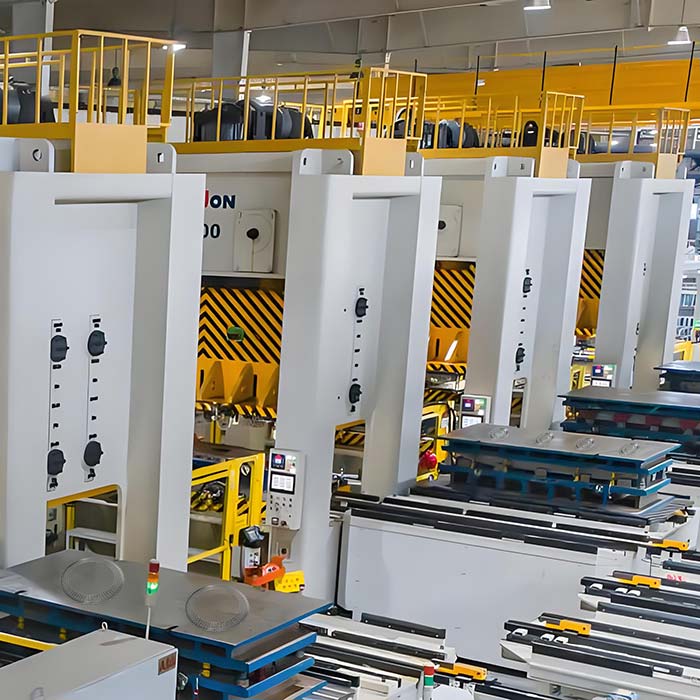
Stator and Rotor Laminations Manufacturer
- We specialize in customized rotor & stator core laminations for motors and generators, Providing various sizes and thicknesses.
- Our advanced stamping for mass production and laser cutting for samples technology, combined with rigorous quality control, ensures precision, accuracy, and reliability.
- Powerful Stamping Ability & Quickly Laser Cutting
- Outer Diameter Range: 30mm~1150mm
- Thickness Range: 0.2mm~0.65mm
- Lower MOQ
- Customization Support
- Certificate: IATF16949
- 30+ patents
What Can We Customize
Dimensions
Diameter, thickness, length, slots, tooths, etc. are customized to perfectly match motor and generator specifications.
Separate purchase
Flexibly purchase stator laminations or rotor laminations, There are 18 punching machines ranging from 110T to 500T that can meet various quantities and sizes of punching.
Assist with mold modification
Will assist in evaluating mold modifications. After the sample verification, if the laminations design needs to be adjusted to meet the final performance requirements of the motor.
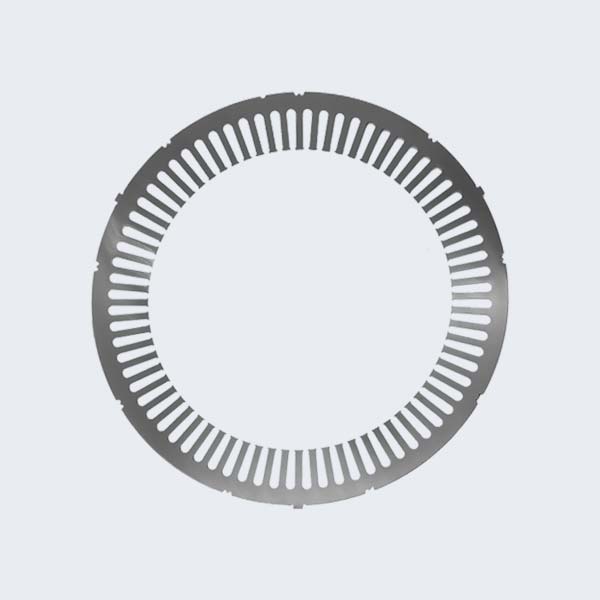
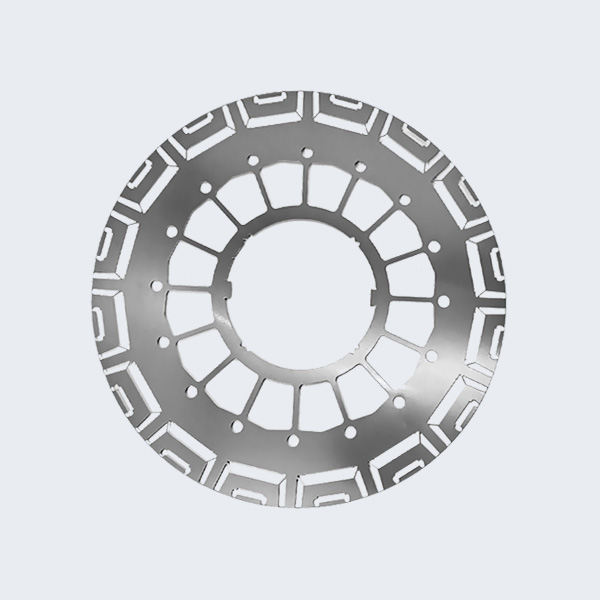
Samples Making
Laser Cutting
- High extreme precision, suitable for intricate designs.
- Fast speed, especially for thin materials.
- Smooth edge quality.
- Applications involve complex geometries with tight tolerances.
Low-Speed Wire Cutting
- Highest precision, perfect for detailed designs
- Speed is the slowest of wire cutting.
- Great surface polish and great edge quality.
- Applications prototypes with extreme accuracy.
Stamping Capabilities
- Our single-slot stamping, compound stamping, and progressive stamping, supported by multiple patented technologies, can meet the requirements of different quantities and designs.
- We have AIDA, SCHULER, and NIDEC high-precision punching machines and excel in batch production of 0.1mm silicon steel and 0.024mm non-alloy laminations.
Compound Stamping
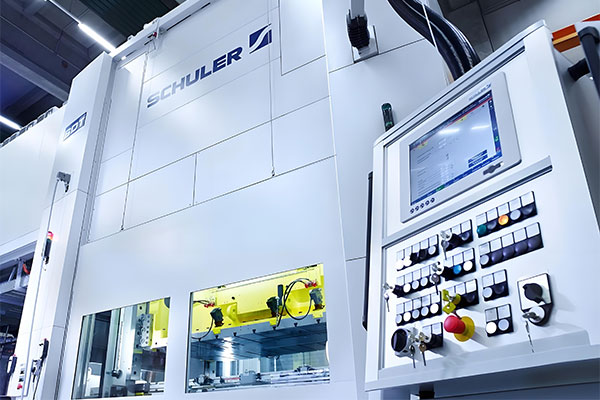
- Punching forces: 110T, 160T, 200T, 250T, 315T, and 500T.
- Achieve small batch production of stator and rotor laminations.
- Low mold cost.
Progressive High-Speed Stamping
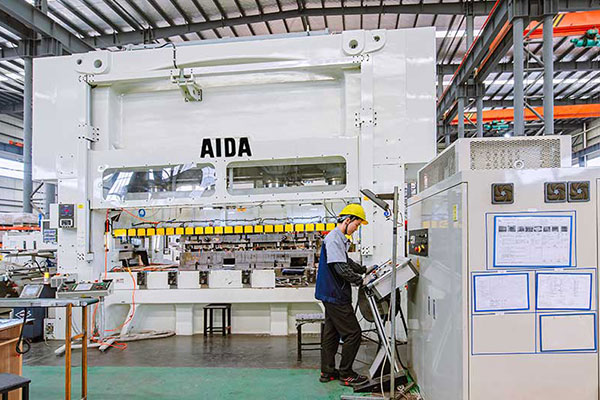
- Punching forces: 80T, 160T, 300T, 315T, 400T, 500T, and 630T.
- Suitable for large batch production of stator and rotor sheets.
- Low products cost.
Single Slot Stamping
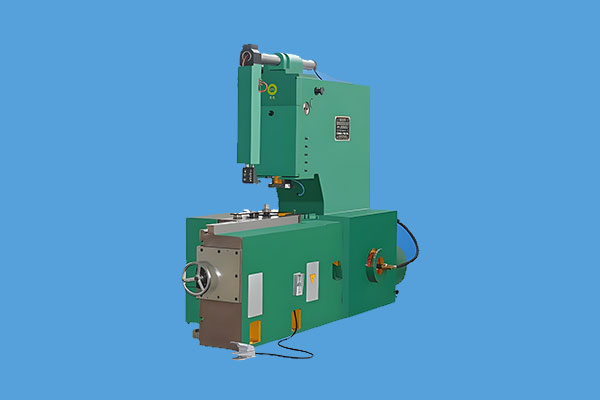
- Punching forces: 45T and 60T.
- Achieve the biggest outer diameter: 1150mm.
- Suitable for less quantity request.
Mold Stamping Process Steps
Our electric motor lamination process typically involves five key steps:
Raw Material Preparation
Source and prepare electrical steel sheets, ensuring consistent thickness, smooth finish, and optimal material quality.
Mold Manufacturing
Design and produce precision molds or dies for cutting laminations accurately, efficiently, and with minimal material waste.
Mold Testing
Loading molds on the punching machine for testing and adjusting, until the products dimensions & tolerance meet the drawings very well.
Stamping
Perform stamping to create laminations with precise dimensions, smooth edges, and excellent accuracy.
Quality Inspection
Conduct thorough inspections, verifying dimensions, surface finish, and insulation to meet industry standards and motor requirements.
Quality Inspection
First-Article Inspection
Self-Inspection
Patrol Inspection
Final Inspection
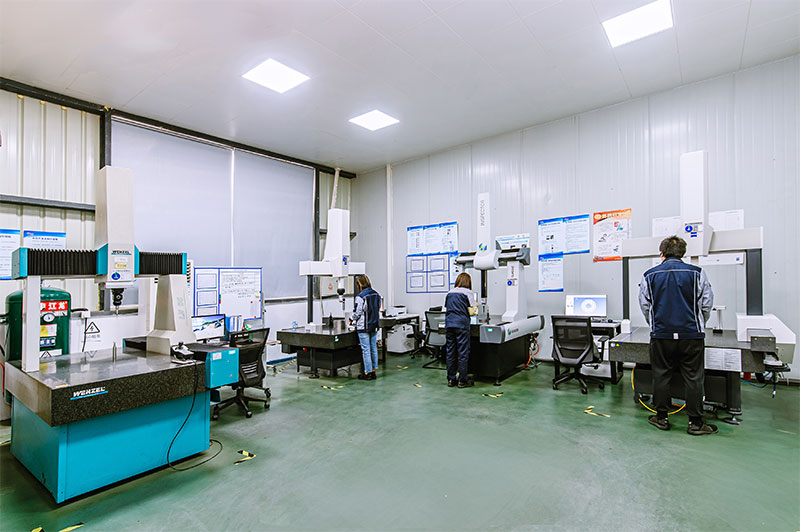
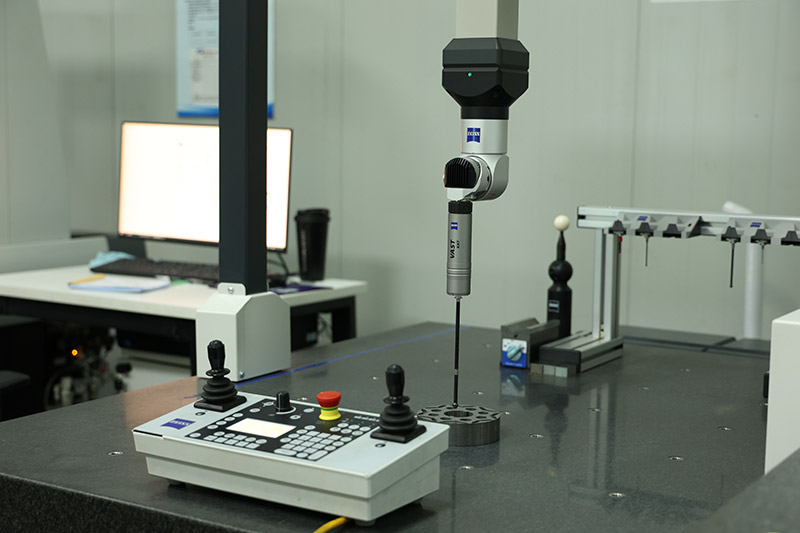
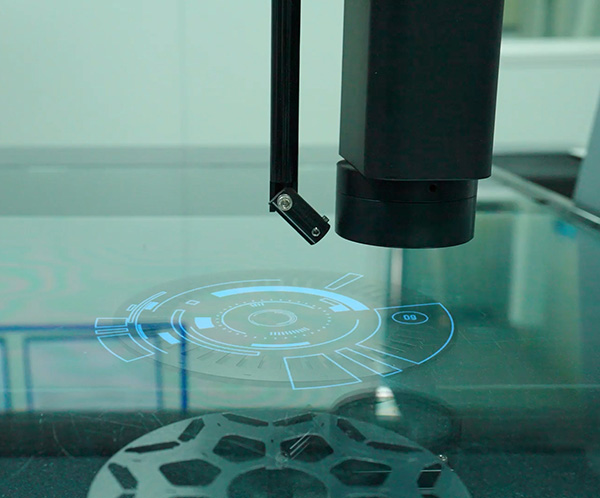
Available Materials
Our electric motor laminations made from silicon steel or amorphous alloy materials offer excellent magnetic properties, low core losses.
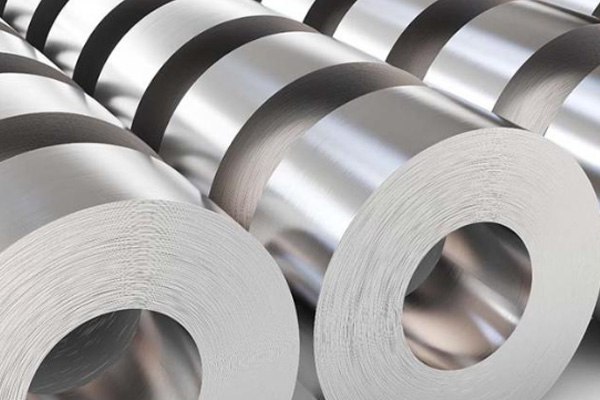
Silicon Steel ( Electrical Steel)
- Thin-gauge options enhance high-frequency performance.
- Excellent insulation reduces eddy current losses.
- Cost-effective and widely used material.
- Ideal for motors, generators, and transformers.
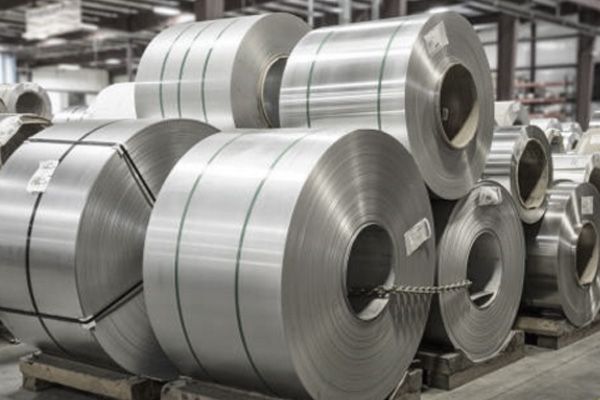
Cobalt Alloys
- High magnetic saturation.
- Superior performance in high-temperature conditions.
- Excellent wear resistance and durability.
- Best for high-performance, precision applications.
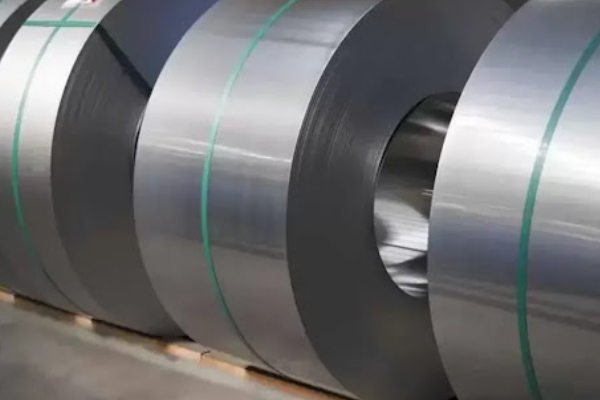
Nickel Alloys
- Exceptional resistance to oxidation and corrosion.
- Superior magnetic properties for advanced designs.
- Reliable under extreme temperature conditions.
- Ideal for specialized motor applications.
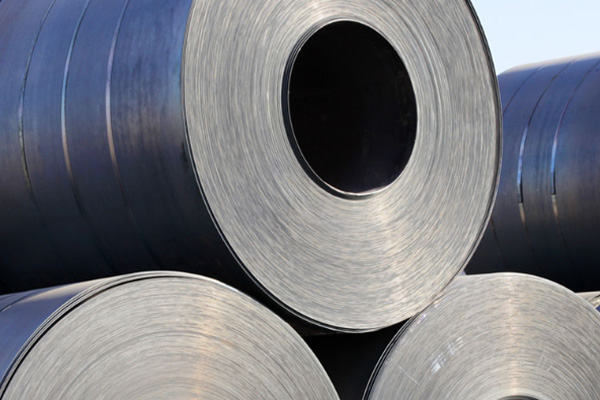
Iron Alloys
- Good magnetic permeability with low losses.
- Cost-effective and commonly available material.
- Suitable for basic motor and generator designs.
- Used widely in general-purpose applications.
Our Global Partners
General FAQs
Quick answers to questions you may have. Can’t find what you’re looking for? Get in touch with us and we’ll provide you with more information.
How do the thickness and material properties of stator core laminations affect performance?
The motor’s overall performance and efficiency are impacted by the lamination thickness. Thinner laminations reduce eddy current losses, while the material properties, such as silicon content, affect magnetic permeability and conductivity, influencing the motor’s overall efficiency.
Can stator and rotor laminations be purchased separately?
Yes, stator and rotor laminations can be purchased separately. You can buy each component according to your motor requirements, ensuring compatibility with the rest of the motor assembly.
How are stator and rotor laminations tested for quality?
Quality testing for stator and rotor laminations includes dimensional checks, magnetic testing, surface inspections for defects, and electrical conductivity tests to ensure the laminations meet strict performance and reliability standards.
What is the delivery time for stator rotor laminations?
After production, stator and rotor laminations are separated with sponges and packed in non-wooden boxes for export. can have its packaging altered to suit the needs of the client. Options include custom box sizes, labeling, and additional protective layers to ensure safe delivery and easier handling.
Can stator and rotor laminations be customized in packaging?
Is there any minimum order quantity requirement for rotor stator lamination?
What factors affect the shipping cost for stator and rotor laminations?
Shipping cost depends on quantity, weight, and delivery method. Express delivery is fastest but costly, while ocean freight is a more affordable solution for bulk shipments. Detailed info is necessary.