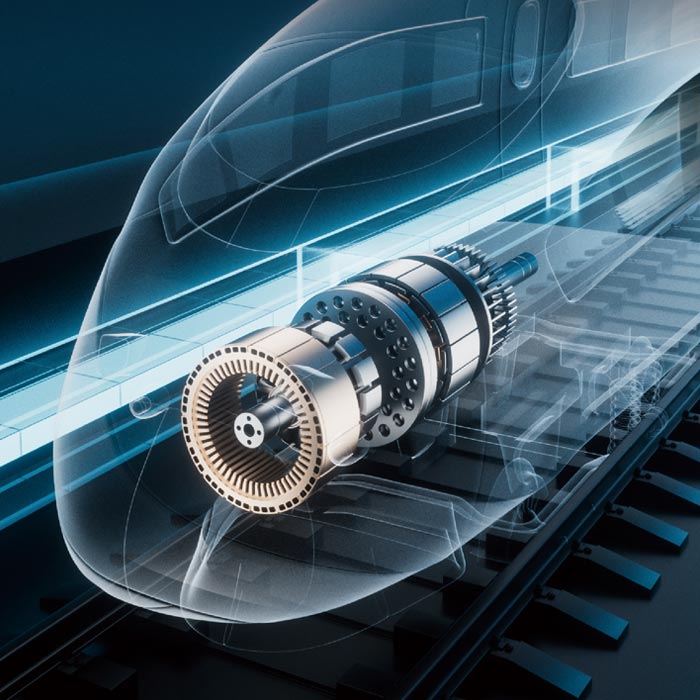
Motor Lamination Stacks for Rail Transportation
- We use high-precision equipment, combining automatic steering manipulators and a gantry-type stamping line, to meet 90-degree turning stamping requirements for rail-crossing products.
- Our full-duplex scrap-falling die structure enables continuous and stable stamping production, enhancing efficiency and output per unit time.
- Stator Range: 300~550mm
- Rotor Range: 210~400mm
- Certification: ISO9001、IATF16949
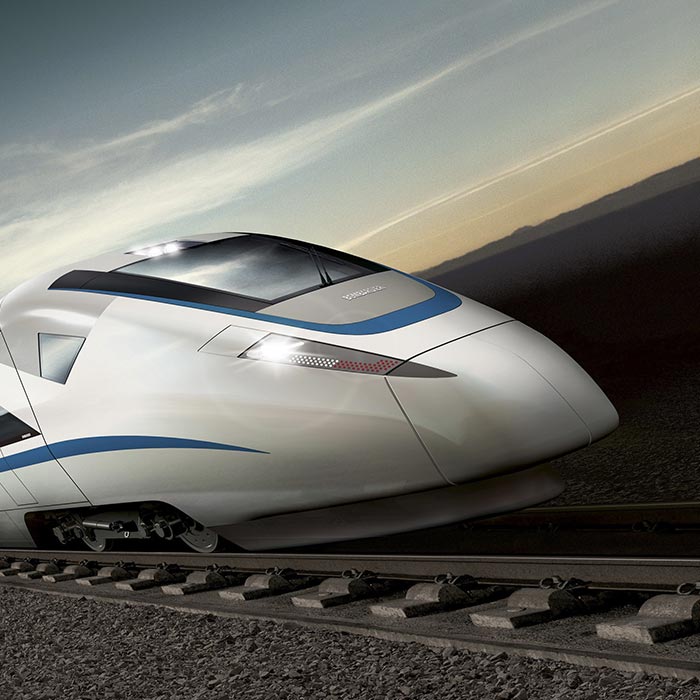
Motor Cores for Rail Transportation Market
- The rail transportation industry is growing rapidly, with increased demand for efficient and reliable systems, including passenger rail, freight rail, high-speed rail, light rail/trams, and subway systems. As cities expand and sustainability becomes more important, rail networks are evolving.
- This growth has led to higher demand for motor cores that ensure performance, energy efficiency, and reliability. Whether you need mass production or single prototype stacks, Gator can provide high-quality solutions with precision.
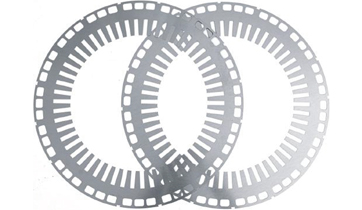
Different Types of Rail Transportation Motor Cores
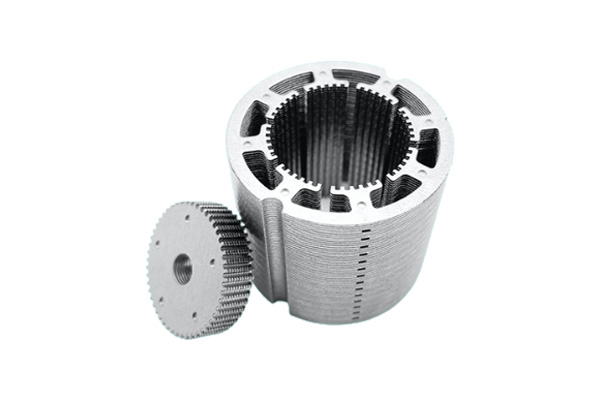
AC Traction Motor Cores
Efficient for high-speed trains, providing power conversion from alternating current to mechanical motion for traction performance and control.
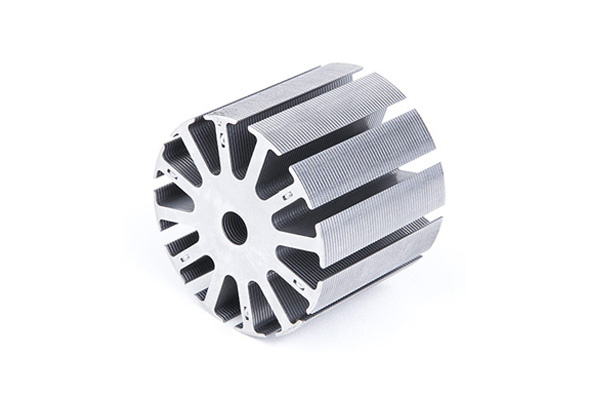
DC Traction Motor Cores
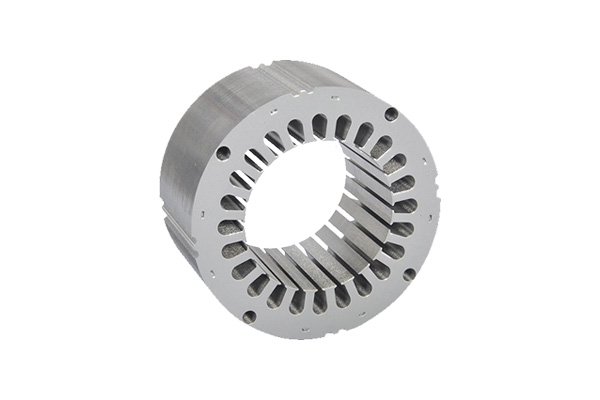
Induction Motor Cores
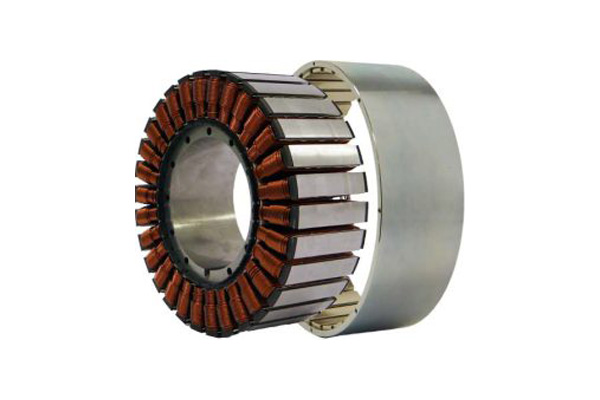
Permanent Magnet Synchronous Motor (PMSM) Cores
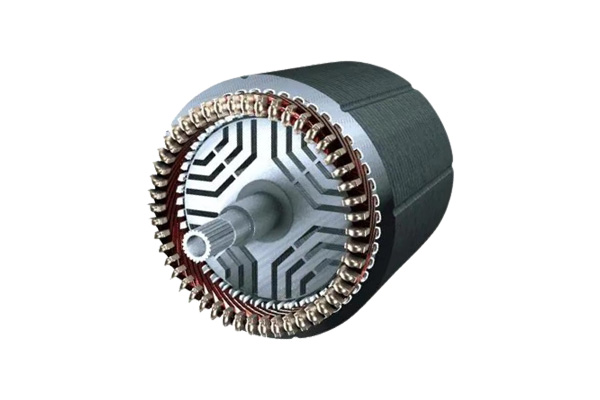
Synchronous Reluctance Motor Cores
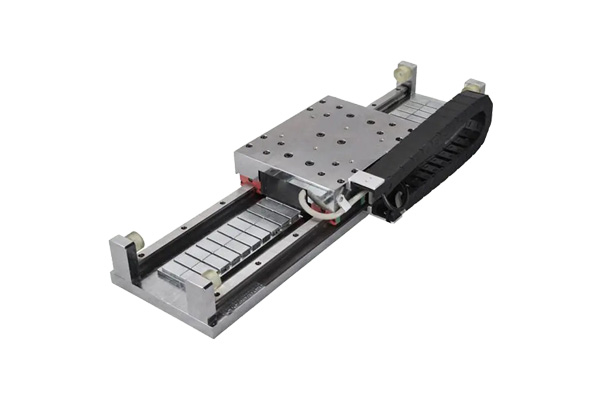
Linear Induction Motor (LIM) Cores
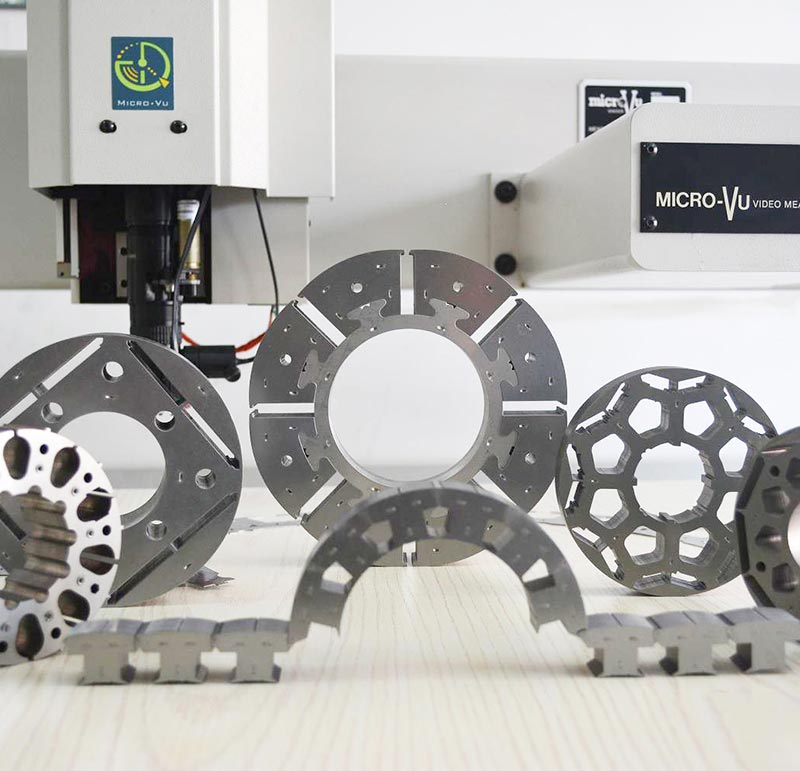
General FAQs
In railway applications, are there specific materials used to manufacture motor laminations?
What are the stamping processes for rail transportation motor cores?
The stamping process involves cutting high-quality silicon steel sheets into precise shapes using dies. Common techniques include single-slot, compound, and progressive stamping for consistent lamination layers.
Can your rotor lamination design be adjusted for different rail systems?
Yes, rotor lamination designs can be adjusted based on specific rail system requirements, such as high-speed trains, light rail, or heavy-duty freight systems, to optimize performance.
What maintenance is required for motor cores in railway applications?
Cleaning, maintaining enough lubrication, and conducting routine wear and tear inspections are essential. Monitoring insulation resistance and checking for electrical issues also help maintain motor core efficiency.
What is the delivery time for your motor cores?
Generally, delivery times vary from 4 to 12 weeks, contingent on order volume and complexity. For special orders, lead times could be longer.